The Critical Angle: Minimum Slope for Metal Roof
At Roof Rescue in Idaho Falls, we’ve seen how the smallest details can make the biggest difference in a roof’s performance. When it comes to metal roofing, one often-overlooked yet critical factor is the roof’s slope, or “pitch”. You might think, “A roof is a roof, right?” Not quite. The angle of your roof plays a huge role in its longevity, durability and ability to protect your home or business, especially here in Idaho Falls with our crazy weather. Slope matters because it directly affects the performance, durability, and proper installation of metal roofs, making it essential to follow standards and manufacturer guidelines.
As your local roofing experts, we’re here to break down the “minimum slope for metal roof” and why it’s non-negotiable for a healthy, long-lasting roof. This isn’t just about aesthetics; it’s about engineering, physics and making sure your investment stands the test of time against everything Mother Nature throws at it. Consulting a qualified roofing contractor is essential for assessing the right slope and ensuring your metal roof is installed correctly.
What is Roof Slope: The Foundation of a Durable Roof
Before we get into the details, let’s define what “roof slope” means. In roofing terms, slope (often called roof pitch) is simply a measure of how steep your roof is. It’s expressed as a ratio, typically in inches of vertical “rise” for every 12 inches of horizontal “run” or horizontal distance. So a 4:12 slope means the roof rises 4 inches for every 12 inches of horizontal distance. The slope is measured by how much the roof rises compared to how far it extends horizontally.
Why is this ratio so important? Primarily it’s about water. Water flows downhill and a sufficient slope ensures rain, melting snow and other moisture sheds off your roof and into your gutters. Without proper slope water can linger, pool and cause a host of problems that compromise your roof’s integrity. Beyond drainage, adequate slope helps with:
Snow Shedding: Crucial here in Idaho Falls, a steeper pitch helps snow slide off, reducing dangerous accumulation and structural stress.
Structural Integrity: Proper slope helps distribute loads (like snow) evenly and ensures the roof system functions as designed.
Longevity: Preventing standing water extends the life of your roofing materials.
Energy Efficiency: While less direct, efficient shedding can prevent moisture issues that can impact insulation performance.
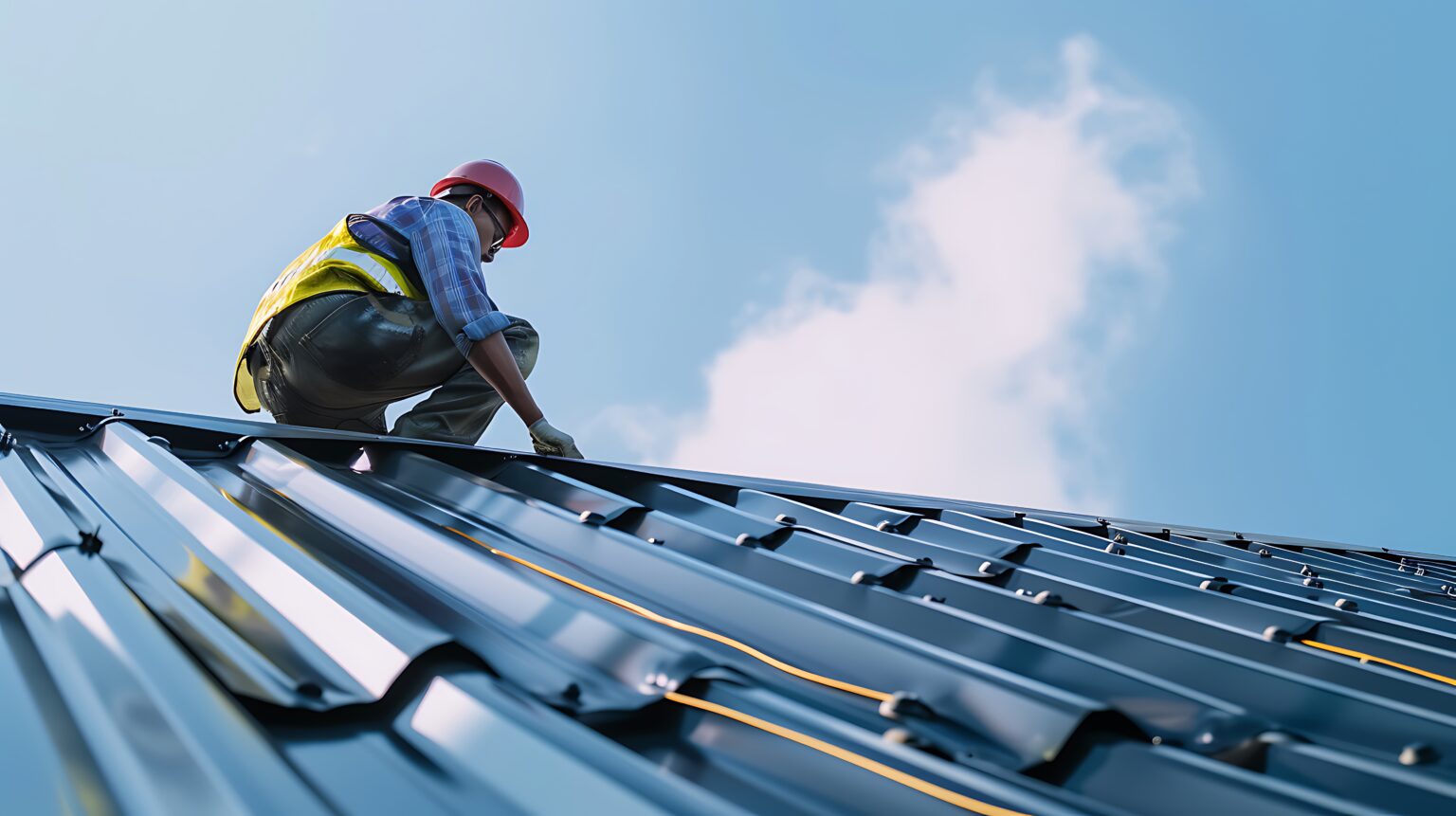
Minimum Slope Explained:
What the Codes and Manufacturers SayWhen we talk about minimum slope for a metal roof, there isn’t a one-size-fits-all answer. It largely depends on the type of metal panel and how it’s installed. Here’s a breakdown of common types and their typical minimum requirements:
Standing Seam Metal Roofs: These are super popular for their sleek look and performance. As a type of metal roofing panel, standing seam panels feature interlocking seams and concealed fasteners, providing superior weather resistance and a virtually watertight system. The pitch for a metal roof is a key factor in ensuring durability and proper water drainage, and standing seam panels are designed to accommodate various slopes depending on the system.
Mechanically Seamed Standing Seam: These systems are super robust and can perform well on very low slopes, often as low as 0.5:12 (1/2 inch rise per 12 inches run) and sometimes even down to 0.25:12 (1/4 inch rise per 12 inches run) when specifically designed and installed with in-seam sealants. This is because the seams are mechanically locked (or double-locked), providing a highly effective protective barrier against water intrusion. Mechanically seamed standing seam panels are a preferred choice for low slope metal roof applications, but always check manufacturer guidelines for the minimum slopes required for your roofing project.
Snap-Lock Standing Seam: While great, snap-lock systems typically require a slightly steeper minimum pitch, often around 2:12 to 3:12, as their locking mechanism is less robust against hydrostatic pressure than mechanically seamed panels. Snap-lock standing seam panels are best suited for moderate slope or steep slope installations, which are ideal for regions with heavy rain or snow due to better water drainage and reduced maintenance needs.
Exposed Fastener Metal Roofs (e.g., Corrugated, R-Panel, PBR Panel): These are common for their cost-effectiveness and durability, where fasteners are visible on the roof surface. Corrugated metal roofs, a specific example of exposed fastener panels, are a durable and affordable option suitable for a range of roof slopes. Due to the nature of exposed fasteners and overlapping panels, they generally require a steeper slope to ensure proper drainage and prevent water from backing up under laps or around fasteners. Choosing the right panel for your roof’s slope and design is crucial for optimal performance and longevity.
Most corrugated and exposed fastener panels require a minimum slope of 3:12. This common roof pitch is referenced in both residential and commercial roofing projects to ensure proper water runoff and durability of the roofing system.
Some profiles, like 7.2 Box Rib or certain R-panels, might be rated for as low as 1:12 if installed with specific sealants and overlapping techniques, but this is less common for general applications. When planning roofing projects, always consider the roof’s slope, roofing material, and the minimum slopes dictated by building codes and manufacturer guidelines. Installing on a lower pitch than recommended increases the risk of leaks and deterioration, so selecting the right slope and panel type is essential for a successful roofing project.
Building Codes: International Building Code (IBC)
Building codes provide the baseline for safe and durable construction. The International Building Code (IBC) is widely adopted, and its requirements for metal roofs are critical. However, it is also important to check your local building regulations, as they may have additional requirements or considerations for your area. For example, IBC 2021 (Section 1507.4.2) states:
Lapped, non-soldered seam without sealant: Requires a substantial 3:12 (25%) slope.
Lapped, non-soldered seam with sealant: Can go as low as 0.5:12 (4%).
Standing-seam metal roof panel systems: Most versatile, can go as low as 0.25:12 (2%).
These are the minimums set by the IBC, but local building codes may specify different or more stringent minimum slopes for metal roofs. At Roof Rescue, we often recommend going above these minimums, especially considering local climate conditions.
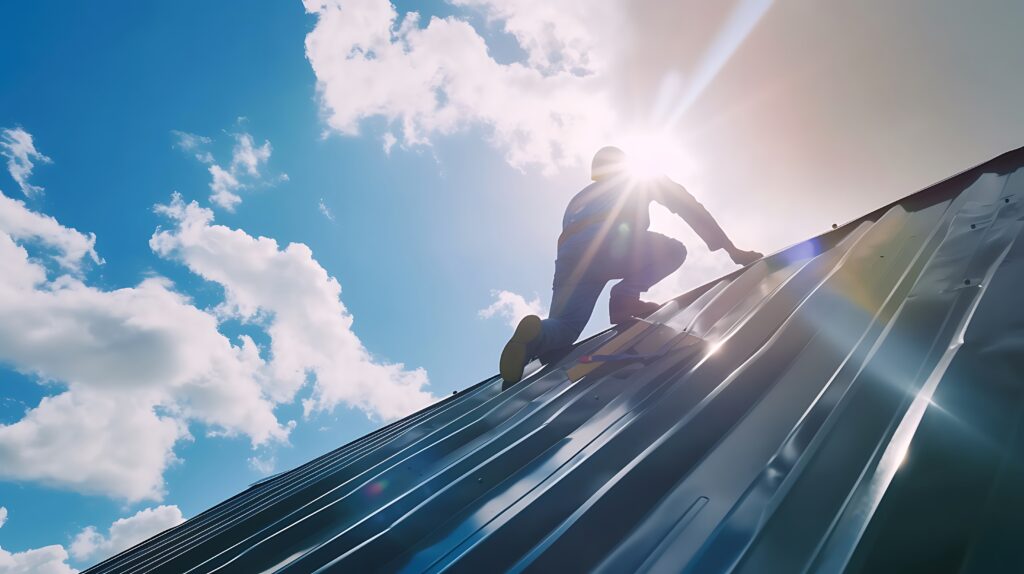
Manufacturer Warranties: Your Contract for Performance
This is where the rubber meets the road. Every metal roofing manufacturer has detailed installation guidelines, and these guidelines always include specific minimum slope requirements for their particular panel profiles. Failing to follow these manufacturer specifications, including the minimum slope, will almost certainly void your roof’s warranty. It is also essential to select the right panel for your roof’s slope, as using the correct panel type is a key part of meeting manufacturer requirements and ensuring your warranty remains valid.
A warranty is your protection against material defects or premature failure. If water consistently pools on a roof installed with insufficient slope, leading to corrosion or leaks, the manufacturer will likely deny any claim, citing improper installation or “faulty building design or construction.” As contractors, our commitment is to install your roof to meet and exceed these critical manufacturer guidelines so your warranty remains valid for decades to come.
Idaho Falls & Your Roof: Why Local Climate Matters
Idaho Falls isn’t just known for its beautiful scenery; we’re also known for our heavy snowfall and temperature fluctuations. This local climate is a big factor when it comes to your roof’s slope. Unlike regions with mild climates and minimal rainfall, where low slope roofs may be more suitable due to their modern appearance, Idaho Falls requires careful consideration of precipitation and snow loads.
Snow Loads: Heavy snow accumulation puts a lot of stress on a roof. A steeper slope helps snow shed more effectively, reducing the load on your structure and minimizing the risk of ice damming. While metal roofs can shed snow on pitches as low as 4:12, in areas with very heavy snowfall, we often recommend slopes up to 7:12 for optimal performance. For any roof, especially those with complex designs or multiple sections within the same roof, it’s essential to ensure adequate drainage to handle heavy precipitation and prevent water buildup.
Freeze-Thaw Cycles: Our climate has frequent freeze-thaw cycles. When water sits on a low-slope roof and freezes and thaws repeatedly, it can exert a lot of pressure, exploit tiny gaps and accelerate material degradation. Proper slope and adequate drainage ensure water evacuates quickly, minimizing this risk. Complex roof structures with different slopes within the same roof require careful planning to manage water flow and drainage effectively.
Choosing a slope that’s right for Idaho Falls’ climate is key to your roof’s long-term health and your peace of mind.
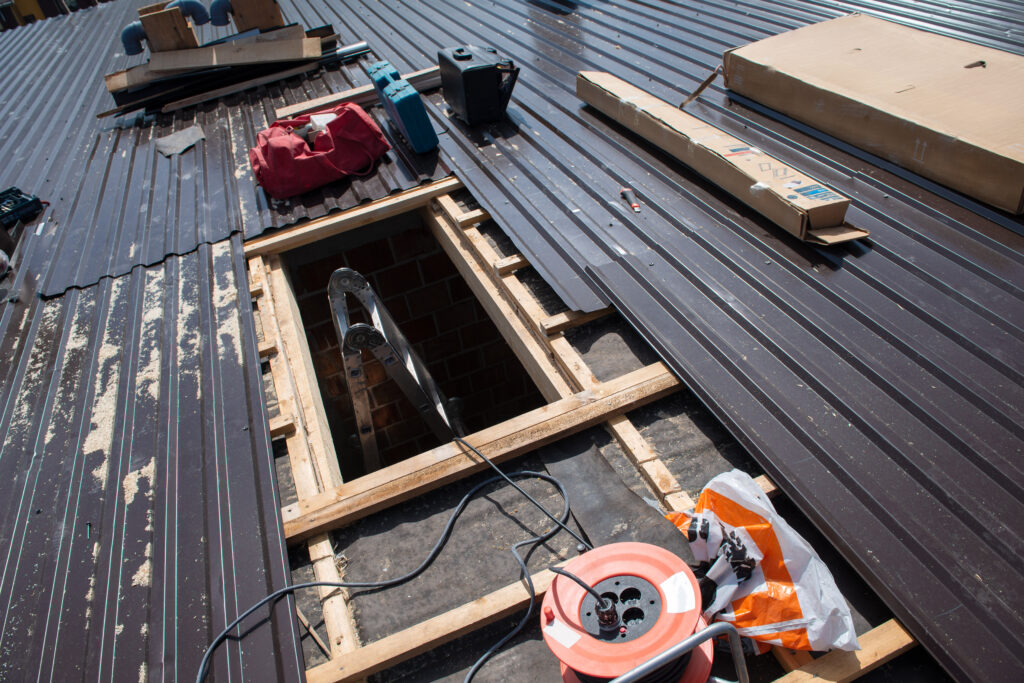
The Consequences of Insufficient Slope: Don’t Get Stuck in the Mud
Ignoring minimum slope requirements can lead to a whole host of expensive and frustrating problems:
- Water Pooling and Ponding: The most obvious issue. Water doesn’t flow off, it collects in depressions on the roof surface. Standing water accelerates corrosion, degrades sealants, and causes premature material failure. Even small amounts of standing water can start to degrade the metal early. Applying lap sealant at seams and joints is crucial to prevent water intrusion in these vulnerable areas.
- Leaks and Water Ingress: Standing water finds its way into the smallest imperfections, seams or fastener points. Leaks can cause damage to your attic, insulation, ceilings, walls and even structural components, mold growth and indoor air quality issues. Using mold resistant materials can help mitigate mold growth resulting from leaks and moisture.
- Accelerated Corrosion and Degradation: Metal is durable but prolonged exposure to standing water can cause oxidation (rust) and other forms of corrosion, shortening the life of your roof panels and fasteners. Especially if the coatings are compromised, you’ll see unsightly blemishes and structural weakness.
- Ice Damming: A big issue in cold climates like Idaho Falls. Ice dams form when snow on a warmer part of the roof melts, runs down to a colder edge (like an unheated soffit) and refreezes. This creates an impenetrable barrier that traps melting water behind it, forcing water under shingles or metal panels and into your home. Insufficient slope makes this worse as water is slow to drain, increasing the chance of refreezing. Ice dams can cause leaks, tear off gutters and fascia, and even bend or dislodge roof panels.
- Compromised Structural Integrity: Repeated water intrusion and the weight of saturated materials can weaken your roof decking and support structure over time, requiring costly structural repairs.
- Voided Warranties: As mentioned, this is a big financial risk. If your roof fails due to insufficient slope, you’ll be paying for repairs or replacement, not the manufacturer.
Beyond the Minimum: Advanced Solutions for Low-Slope Metal Roofs
Installing a low slope metal roof involves careful consideration of slope, drainage, and material compatibility to ensure long-term performance and durability.
For architectural designs or building types that really need very low-slope metal roofs, there are specialized solutions that go “beyond the minimum” to ensure watertight performance. In some cases, buildings may feature sections with different slope, requiring tailored solutions for each area:
Mechanically Seamed Standing Seam Systems: These are the workhorses of low-slope metal roofing. Their robust, mechanically seamed (or double-locked) panels create an incredibly strong, weathertight seal. Systems like the Tite-Loc Plus panel are excellent examples, featuring a tall 2-inch leg height and a concealed fastener, floating clip design. They can achieve pitches as low as 0.5:12, offering great protection even with minimal slope. Their integrated sealant and precision engineering make them ideal for challenging low-pitch applications. The ability of hydrokinetic roofs to move water quickly and efficiently contributes to their performance on low slopes.
High-Performance Underlayments: Beneath the metal panels, the right underlayment is your primary line of defense. It is also important to ensure the roof structure is adequate to support the chosen low-slope metal roofing system and complies with local building codes.
Self-Adhering Membranes (Peel-and-Stick): These are essential for low-slope applications. Made from rubberized asphalt or butyl, they create a true secondary watertight barrier, adhering directly to the roof deck. They are highly resistant to water penetration, great for ice dam protection, and an effective air barrier.
Synthetic Underlayments: While not self-adhering in the same way, high-quality synthetic underlayments offer superior durability, tear resistance and moisture effectiveness compared to traditional felt paper. They can handle higher temperatures and often come with longer lifespans, providing reliable moisture protection even if a primary seal is compromised. Traditional felt is not recommended for low-slope metal applications as it breaks down when exposed to standing water.
Precision Sealing and Flashing: Every penetration, seam and edge on a low-slope roof must be sealed and flashed. High-quality sealants, specialized tapes and custom-fabricated flashing details are required to prevent water ingress where the slope isn’t enough to simply shed water by gravity alone. This includes proper overlaps and sealing at panel ends and trim.
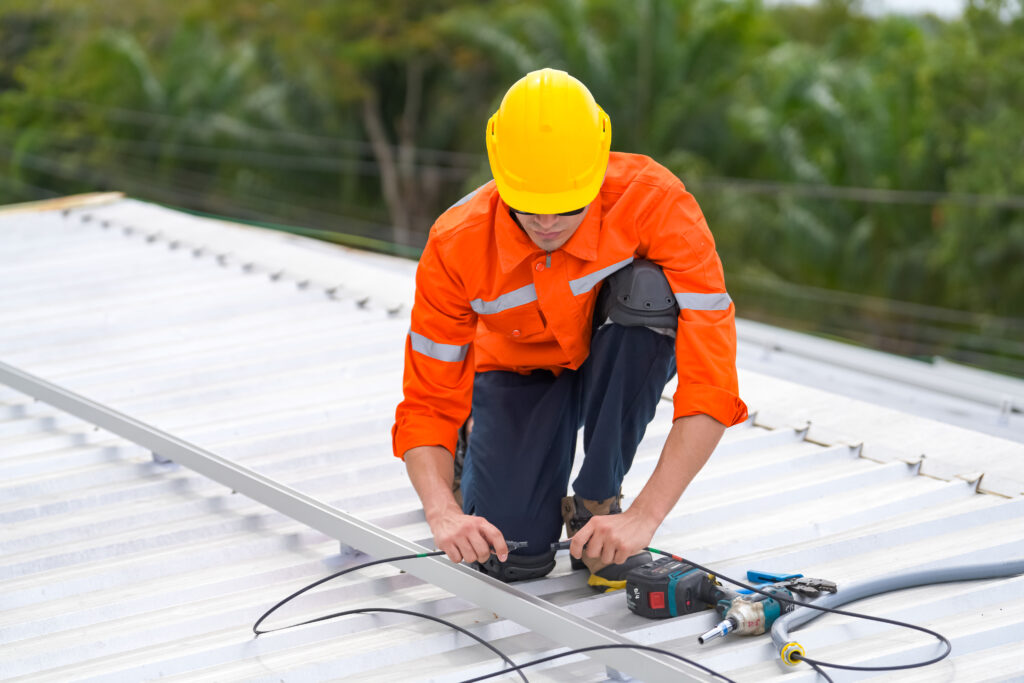
Built to Last: Best Practices for Drainage
Optimal drainage on any metal roof, regardless of slope, requires best practices in design and installation:
1. Thoughtful Design:
Slope for Climate: As mentioned, always factor in local weather patterns like Idaho Falls’ snow loads. A slope above the minimum is often a good choice for long-term performance.
Roof Geometry: Avoid valleys, complex intersections or areas that could create reverse slopes or depressions where water can collect. Design for clear drainage paths.
Gutters and Downspouts: Ensure gutters are the right size, pitched and clear of debris to handle the volume of water shed by the roof. Downspouts should be placed to direct water away from the foundation and high-traffic areas.
2. Installation Quality:
Panel Alignment: Panels must be installed straight and square to prevent gaps or misalignments that can trap water or allow wind uplift.
Fastening: Fasteners must be installed correctly, typically through the high points of exposed fastener panels, with washers compressed to create a watertight seal. For concealed fastener systems, clips must be engaged and secured.
Seam Integrity: For standing seam, mechanical seaming must be uniform, complete and crimped. For exposed fastener systems, panel overlaps must be sealed with butyl tape or a continuous bead of sealant to create a durable bond.
Flashing: All flashing details around chimneys, skylights, vents and wall intersections must be custom-fitted, sealed and installed in a “shingle fashion” (overlapping to shed water) to create redundant barriers against water intrusion. This is where inexperienced installers fail.
Underlayment: Underlayment should be applied smooth, wrinkle-free and with proper overlaps (e.g., 6-inch horizontal and 12-inch vertical overlaps and proper trim at ends) to create a continuous secondary moisture barrier.
3. Material:
Panel Profile for Slope: Choose a metal panel profile designed and warranted for your roof’s intended slope. Don’t try to force a panel meant for a steep pitch onto a low-slope roof.
Metal Roofing Material: Selecting the appropriate metal roofing material is essential, as different materials may have specific slope requirements to ensure proper drainage and long-term performance.
Sealants and Fasteners: Use only marine-grade or roofing-specific sealants and long-life, corrosion-resistant fasteners, often with special coatings.
Durable Coatings: Make sure the metal panels have tough, fade-resistant and corrosion-resistant coatings (like Kynar 500® or Hylar 5000®) for the Idaho Falls climate and potential standing water on low slopes.
The Roof Rescue Guarantee: Long-Term Value and Peace of Mind
Following slope guidelines and manufacturer specifications isn’t just about meeting codes; it’s about protecting your investment and your property. By working with Roof Rescue you get:
Longer Roof Life: A properly sloped and installed metal roof can last 40-70 years, significantly outperforming asphalt shingles in both lifespan and durability, and offering one of the lowest life cycle costs among roofing materials.
Less Maintenance & Repair: Efficient drainage prevents the issues that lead to costly repairs, saving you money and hassle over the years. Metal roofs are low maintenance, and proper slope enhances that benefit.
Warranty Validity: You have the full backing of the manufacturer’s warranty, protecting you from material issues and your investment is secure.
Increased Property Value: A high-performing, beautiful metal roof adds value and curb appeal to your home or business, and is sustainable too.
Peace of Mind: Knowing your roof is installed to withstand Idaho Falls weather offers ultimate security and protects your most valuable asset.
Conclusion
The minimum slope for a metal roof is more than just a technical requirement; it’s a fundamental principle of watertight roofing. At Roof Rescue in Idaho Falls, we understand metal roofing and the Idaho Falls climate. We follow manufacturer specifications, exceed building codes and best practices to ensure your metal roof performs for decades.
Don’t leave your roof to chance. If you’re considering a new metal roof or have questions about your existing one, contact Roof Rescue today. We’ll give you the angle on a secure roof.

Mark Franklin, owner of Roof Rescue in Idaho Falls, Idaho, has been a trusted name in roofing since 2014. Serving Idaho, Montana, Wyoming, and Utah, Roof Rescue specializes in commercial and residential roof replacement and installation. Recognized for community initiatives like the “Operation Roof Rescue” program, which provides free roofs to local heroes, Mark combines professionalism with a passion for giving back. With 16 years of industry experience, an A+ Better Business Bureau rating, and glowing customer reviews, Mark’s leadership embodies quality and community-focused service.