Introduction: Why Chimney Flashing is More Important Than You Think
A home’s structure is built on components that, although minor or out of sight, are critical to its long term health. Among these, chimney flashing stands out. This material that seals the gap between the exterior chimney and the roof is considered one of the simplest parts of a chimney system. But don’t let its simplicity fool you. When damaged, chimney flashing can cause serious and widespread problems throughout a home.
This is a hidden vulnerability. Often overlooked during routine home maintenance, its failure can trigger a chain reaction of costly consequences that go far beyond a simple leak. The initial perception of flashing as a simple part can lead homeowners to underestimate its importance. That underestimation often results in neglect and minor issues becoming major structural damage, mold growth and big bills.
Understanding the role of chimney flashing is the first step in protecting your home. For complete protection and peace of mind, identifying and fixing these hidden vulnerabilities requires specialized expertise. Roof Rescue is your trusted partner to repair chimney flashing and get the job done.
What is Chimney Flashing: Your Home’s First Line of Defense
What is Chimney Flashing?
Chimney flashing is a specialized material or construction technique that creates a watertight seal at the junction where the chimney meets the roof. Its main job is to keep water out of the building through this point of penetration. Typically made of durable, corrosion resistant metals like aluminum, copper or stainless steel, flashing is installed around the base of the chimney. This barrier directs rainwater and melting snow away from the chimney and onto the roof surface, protecting the entire structure.
Why Proper Flashing is Key
Proper flashing is more than just keeping water from dripping into your home. It’s critical to the overall performance and protection of the entire building envelope.
- Waterproofing: The main and most important job of chimney flashing is to create a watertight seal between the chimney and the roof to prevent leaks. Without this barrier, water can get into gaps or cracks around the chimney and cause leaks that show up as water damage, wood rot, mold growth and even structural issues in the home
Roofing Material Protection: Flashing directs water away from the most vulnerable areas where the chimney meets the roof. This prevents water from seeping under the roofing materials and slows down the deterioration process of shingle damage, wood rot and the weakening of the roof deck itself.
Chimney Structure Preservation: Water infiltration is a big threat to the chimney structure. Over time, moisture can cause mortar joints to deteriorate, metal components to rust and the overall chimney structure to weaken. Proper flashing ensures water is always directed away and preserves the chimney’s strength and longevity.
Energy Efficiency: Beyond preventing leaks, chimney flashing also contributes to a building’s energy efficiency. A sealed chimney minimizes drafts in winter and prevents hot air from entering in summer. This results to a more stable indoor climate and reduced energy consumption.
Cost Savings: Investing in proper chimney flashing is a smart financial decision. By preventing water damage and all the associated problems, homeowners can avoid more costly repairs and extensive renovations down the line. It’s a long term investment in the chimney, the roof and the overall structural integrity of the property. Since these protective functions are interconnected, a flashing repair is not just fixing a symptom like a leak but restoring multiple layers of defense for the entire home system and increasing its long term resilience and value.
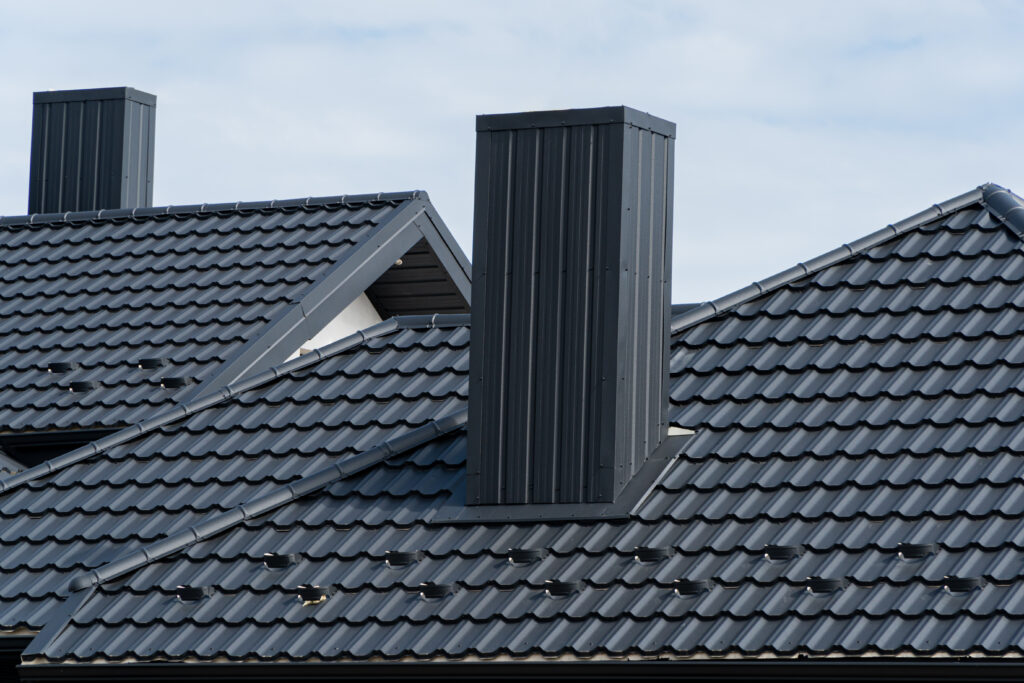
Chimney Flashing Components
Chimney flashing systems are composed of several interconnected components to achieve a watertight seal. The main components are step flashing and counter flashing. Step flashing is individual L-shaped metal pieces interwoven with the roof shingles. These are installed in a cascading manner to allow water to flow down and away from the chimney onto the roof surface. When installing step flashing, each piece must be bent and overlapped at the top corner of the chimney to create a seal and prevent leaks. Counter flashing covers and protects the step flashing. Counter flashing is a vertical piece of metal either embedded in the chimney’s mortar joints or fastened to the chimney itself. It’s often installed along the top edge of the flashing assembly, overlapping the step flashing to create a finished waterproof seal and prevent water from getting behind the flashing. The counter flashing overlaps the step flashing to create a sealed barrier that prevents water intrusion. This layered and overlapping design is key to a durable and effective seal.
Chimney Flashing Materials: Choosing the Right Protection
Choosing the right materials for chimney flashing is crucial to its performance and longevity. Various metals are used, each with its own properties that affect its suitability for this application.
When cutting flashing materials, tools like a circular saw with a diamond blade or a utility knife are used depending on whether you’re working with masonry, metal or other roofing components.
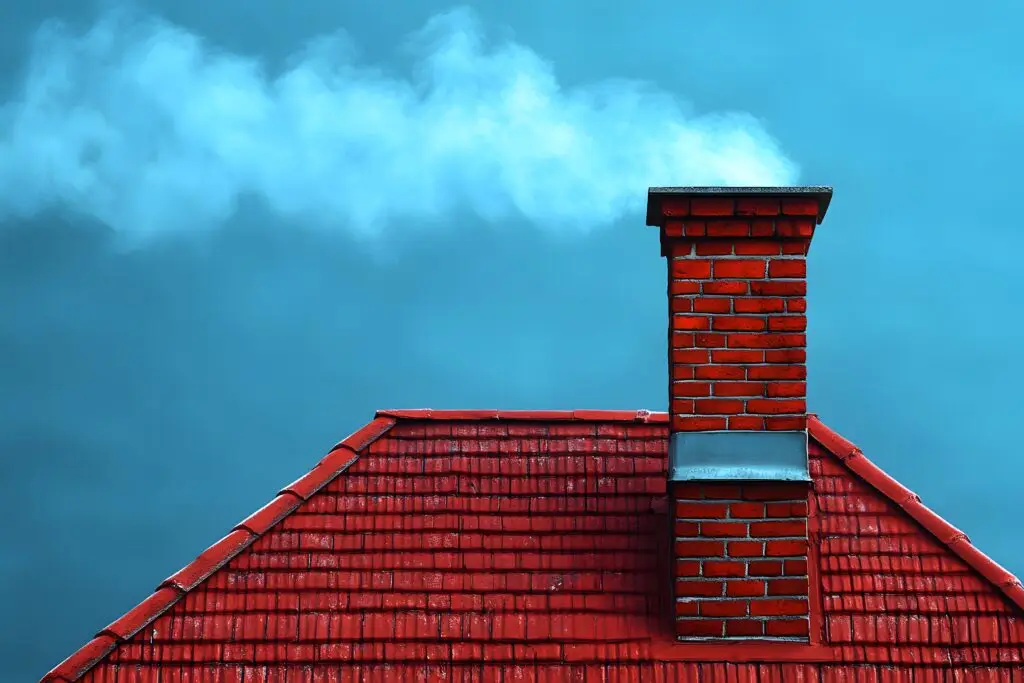
Materials Overview
Copper: Considered an excellent choice for chimney flashing, copper is highly malleable and easy to shape and work with. It can withstand wide temperature fluctuations without buckling or warping. Copper doesn’t react with mortar even when embedded in a wet mix. It may stain surrounding brickwork but that’s not a big issue.
Stainless Steel (Type 304): Type 304 stainless steel is also a good material for chimney flashing. Less malleable than copper, it can still be formed and worked. Stainless steel has excellent resistance to reactions with chimney materials and temperature and water resistance. The Brick Industry Association recommends a minimum of 0.01 inch (0.25mm) thickness for stainless steel flashing.
Galvanized Steel: Galvanized steel is sometimes used as chimney flashing but is not recommended. Durability depends on the thickness of the zinc coating applied during manufacturing; thicker is better. But during bending of galvanized steel with sufficient zinc thickness, the coating cracks. This exposes the base metal to the elements and causes rusting and staining of the chimney and surrounding roof areas. For this reason, galvanized steel is generally not recommended as primary chimney flashing material.
Aluminum: Aluminum is used for chimney flashing, especially newer coated versions. These coatings are designed to counteract the reactive properties of aluminum with the alkali content in fresh mortar which can cause flashing deterioration due to ionic salts.
Elastomeric Flashing Repair: When flashing at the roof/chimney intersection is missing or damaged, an elastomeric flashing repair is a great option. This material has many advantages: extreme durability, fast installation and cost-effective for the homeowner. Elastomerics are beneficial because they accommodate the huge movement that occurs at this intersection as the chimney and roof expand and contract with temperature changes and maintain a watertight seal. This is an evolution in repair materials, a modern solution for a specific problem.
Compatibility Issues
A critical aspect of flashing installation often overlooked by those without specialized knowledge is material compatibility. Experts warn: don’t mix metals. This is due to galvanic action. When rainwater runs off copper flashing, it can chemically corrode galvanized sheet metal and stainless steel. Even if individually durable, incompatible metals used together can cause premature failure of the flashing system. So you must choose a flashing material that is compatible with all other components of the roof system.
And don’t forget about fasteners. Copper flashing should only be attached with copper nails, galvanized sheet metal with hot-dipped galvanized nails. Use the right type of nail, roofing nails, and hammer them in at regular intervals for proper installation and long-term durability. Even the underlayment matters: red rosin paper is recommended under copper flashing but not roofing felts as the bitumen in the felts reacts with the copper. These technical details show that flashing installation is not just about mechanical attachment but involves material science to ensure long-term integrity. A professional has this specialized knowledge so all components work together to prevent future damage from incorrect material pairings.
Trouble Signs: How to Spot Damaged Chimney Flashing
Recognizing the signs of damaged chimney flashing is key to early intervention and preventing minor issues from becoming major and costly problems. Old flashing or existing chimney flashing is a common source of water intrusion and should be inspected regularly. The symptoms of flashing damage can be many and varied and affect different parts of the home.
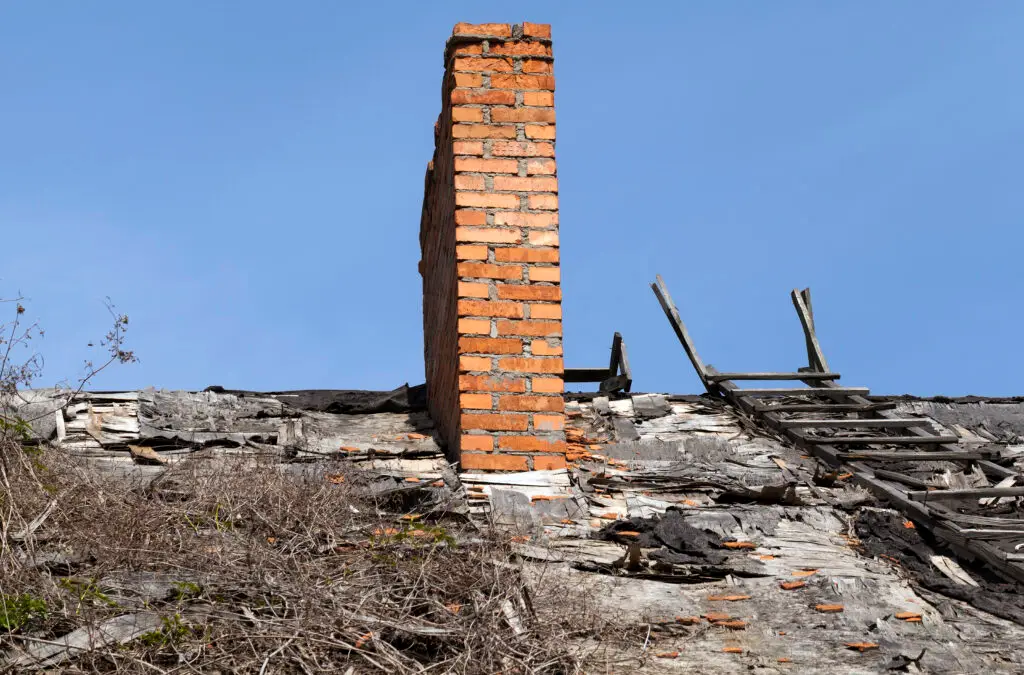
Full List of Symptoms
Water Stains on Ceilings and Walls: One of the most common and obvious signs of flashing failure is water stains, usually brown or yellow discolorations, on ceilings and walls especially those near the chimney. These stains mean water is actively seeping through the compromised flashing and into the home, especially in areas not covered by flashing, making them more prone to water damage.
Dampness or Musty Smell: A damp feeling or a musty odor in the attic or around the fireplace area means moisture is getting in. This moisture creates an environment for mold and mildew growth and indoor air quality issues.
Visible Rust or Corrosion: Chimney flashing, made of metal, will rust or corrode over time from exposure to the elements. Any visible signs of deterioration on the flashing itself or rust in the firebox means the material is failing.
Cracks or Gaps in the Flashing/Caulking: A direct inspection of the area around the chimney will show visible openings, brittle or cracked caulking or sections of the flashing that have lifted or pulled away from the chimney or roof surface. These breaches are direct water entry points.
Leaking During Heavy Rain: The most obvious and alarming sign is water dripping inside the home during heavy rain, especially near the chimney. Wind driven rain can force water into gaps around the chimney if the flashing is not installed properly and leak even when the flashing looks intact. This means the chimney flashing is not doing its job.
Peeling Paint or Wallpaper: Moisture seeping through compromised flashing can weaken the adhesive behind interior paint or wallpaper and cause bubbling, peeling or complete detachment of finishes near the chimney.
Mold or Mildew Growth: Mold or mildew on walls, ceilings or in the attic space especially near the chimney is a sign of a damp environment created by water leaks. Beyond being unsightly, mold can be harmful to health.
Discolored or Crumbling Bricks/Mortar: Water damage can cause staining on the chimney bricks or cause them to crumble over time. Deteriorating or crumbling mortar joints between the bricks can compromise the flashing and allow water to enter the chimney structure.
Damaged Roof Shingles Near the Chimney: Water under the roof shingles near the chimney can lift, curl, make them brittle or even missing. This means the flashing is not diverting water properly.
Debris Accumulation: Inadequate flashing can cause water to pool around the chimney base and debris like leaves or twigs to accumulate. Areas not covered by flashing are especially prone to this pooling which worsens water damage.
Sagging Roofline Near Chimney: A sagging roofline near the chimney is a severe sign of extensive water damage that has weakened the roof structure. This is a red flag that needs immediate attention.
Ice Dams: Ice dams near the chimney means heat is escaping through the flashing and melting snow that refreezes at the colder roof edge. This is a flashing problem and heat loss.
Increased Energy Bills: A sudden and unexplained increase in energy consumption might be due to heat escaping through compromised flashing which means a breach in the home’s thermal envelope.
Animal Intrusions: Gaps or damage in chimney flashing can provide entry points for nuisance animals like birds or squirrels to get into the home or attic space.
These signs show that chimney flashing failure is not just one problem but a multitude of issues that can affect the home’s structure, indoor air quality, energy efficiency and pest control. A small breach in this waterproofing barrier can trigger a domino effect throughout the entire building envelope. Recognizing these signs early is crucial as prompt action can prevent extensive water damage and more expensive repairs.
Category | Signs | Description |
---|---|---|
Visual Cues | Water Stains on Ceilings/Walls | Brown or yellow discolorations, especially near the chimney. |
Visible Rust/Corrosion on Flashing | Deterioration of metal flashing or rust in the firebox. | |
Cracks or Gaps in Flashing/Caulking | Visible openings, brittle caulk, or lifted sections. | |
Discolored or Crumbling Bricks/Mortar | Masonry staining or deterioration. | |
Damaged Roof Shingles Near Chimney | Shingles lifting, curling, or becoming brittle. | |
Peeling Paint or Wallpaper | Bubbling or peeling of interior finishes near the chimney. | |
Mold or Mildew Growth | Visible fungal growth on walls, ceilings, or in the attic. | |
Debris Accumulation | Leaves or twigs pooling around the chimney base, especially where flashing fails. | |
Sagging Roofline Near Chimney | A visible dip in the roof structure. | |
Olfactory Cues | Dampness or Musty Smell | A persistent odor indicating moisture intrusion. |
Other Indicators | Leaking During Heavy Rain | Water dripping inside during storms, often due to poor flashing installation. |
Increased Energy Bills | Heat loss through gaps causes unexpected spikes in energy costs. | |
Animal Intrusions | Signs of pests entering through flashing gaps. |
The Cost of Neglect: Why Ignoring Flashing Damage is a Risky Business
Ignoring damaged chimney flashing is a financially dangerous decision that can lead to a rapid and exponential increase in problems and repair costs. Timely flashing repairs are crucial to prevent minor issues from becoming major structural problems. What might start as a small, inexpensive fix can quickly become a major, expensive structural problem, health hazard and property devaluation.
Escalating Damage
Structural Deterioration: Water is a powerful force and persistent water intrusion through faulty flashing can weaken critical structural components of a home. Roof timbers can rot, the underlying framework can be compromised and the entire building structure can be severely damaged.
Interior Damage: The visible effects of neglected flashing often appear first inside the home. Water leaks cause unsightly and costly damage to interior ceilings, walls and finishes. This can require extensive repairs including repainting, drywall replacement and even floor repairs far beyond the initial flashing issue.
Chimney Structure Damage: The chimney itself is very vulnerable. Continuous exposure to moisture can cause mortar joints to deteriorate and masonry to crumble. Metal components in the chimney can rust and the entire chimney structure can weaken and potentially collapse over time.
Health Risks
Moist environments created by water leaks are a perfect breeding ground for mold and mildew. The presence of these fungi is not only unsightly and damaging to building materials but also a health risk to occupants, potentially exacerbating respiratory issues and allergies. Long term exposure to mold can have serious consequences for indoor air quality and occupant well-being.
Financial Consequences
The cost of ignoring damaged flashing is significant and illustrates the pay now or pay much more later principle. A small issue that could have been fixed with a simple reseal for as little as $200 by a professional can quickly escalate. If the flashing becomes severely damaged or corroded a full replacement is needed which can cost from $400 to over $1,600 and potentially up to $2,000 for larger or stone chimneys.
Furthermore, compromised flashing can lead to premature deterioration of the entire roof and may require costly re-roofing projects that could have been avoided with timely flashing repair. The initial investment in proper flashing is designed to save homeowners from these much more expensive repairs and renovations down the line. This cost curve accelerates and shows that proactive maintenance and professional intervention are not just expenses but critical financial safeguards against growing problems.
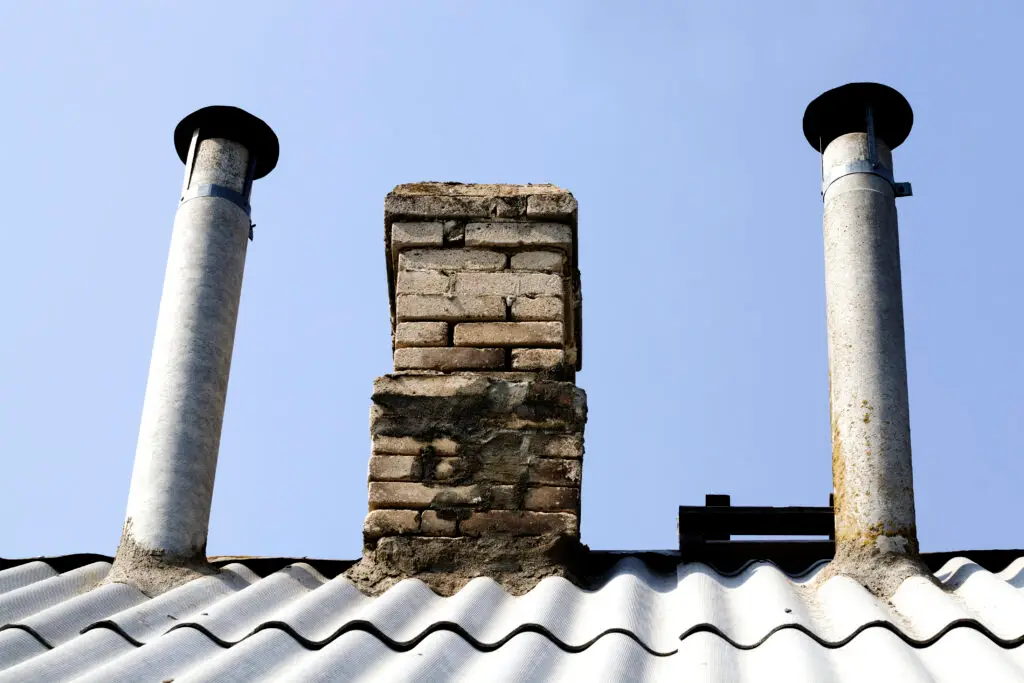
The Professional Approach: What Chimney Flashing Repair Entails
Fixing chimney flashing requires expertise, specialized tools and adherence to strict safety protocols that go beyond a DIY project. Installing chimney flashing requires expertise to ensure a tight waterproof seal, especially when working with a new chimney or upgrading an existing one. Proper installation involves measuring and laying the first piece of base flashing, then attaching and nailing each subsequent piece so that it overlaps the previous piece for a secure seal. You need to add step flashing along the sides of the chimney and install a chimney saddle to divert water away. Each flashing piece must be attached and fitted tight to prevent leaks, with attention to attaching and nailing for long term protection.
Why Professional Expertise is Needed
Chimney flashing roof repair is a skilled trade that requires precise design, meticulous installation and specialized tools. Working on roofs, especially those with steep pitches, is inherently risky. Professionals have the necessary safety gear such as harnesses, non-slip shoes, chicken ladders and scaffolding and are trained in their use. This ensures the work is done without putting the homeowner or the property at risk.
Beyond safety, professional roofers have a deep understanding of the technical details, such as material compatibility and galvanic action. They know which metals can and cannot be mixed to prevent premature corrosion. They are also skilled at complex installation techniques such as layering step flashing and counterflashing and cutting grooves into mortar joints for a secure, long lasting, watertight seal. This knowledge and experience ensures the repair is not just a temporary fix but a long term solution for the home.
The Professional Repair Process (Roof Rescue's Method)
A professional chimney flashing repair follows a systematic multi-step process to ensure thoroughness and effectiveness:
Thorough Inspection & Assessment: The process starts with a thorough inspection of the existing flashing system. This involves identifying all signs of damage, such as cracks, rust, loose sections, or water intrusion, to determine the extent of the problem and the scope of repairs.
Safe Removal of Damaged Flashing: Any old, ineffective or corroded flashing is cut away and removed. This step requires precision to avoid damaging surrounding roof shingles or the chimney structure itself. Old roofing cement and debris is also scraped away to ensure a clean surface. Throughout this stage protective gear including gloves and eye protection is essential.
Area Preparation & Cleaning: The area where the new flashing will be installed is cleaned using a wire brush to remove any dirt, rust or old cement. This is crucial to ensure proper adhesion of the new materials and a watertight seal. During this stage professionals also inspect for any underlying wood rot or water damage that may have occurred.
Precise Measurement & Cutting of New Flashing: Measurements of the roof slope and chimney dimensions are taken to ensure the new flashing pieces fit snugly. This includes cutting base, step, cap and saddle flashing pieces to allow for correct overlapping which is crucial to direct water away from the structure.
Strategic Positioning & Installation: The newly cut flashing pieces are positioned around the chimney. Installation typically starts with the base flashing, then step flashing along the sides and finishes with the counterflashing at the top. Counterflashing is often embedded into the chimney’s mortar joints to create a solid seal.
Secure Fastening: The flashing is then fastened to both the roof and the chimney using the appropriate fasteners. For example, copper flashing requires copper nails, galvanized sheet metal uses hot-dipped galvanized nails. Fastening is only done at the edges to minimize the creation of holes that could become entry points for water. Masonry anchors may be used for cap flashing embedded into mortar joints.
Comprehensive Sealing: A bead of high-quality roofing cement or caulk is applied along all edges and seams of the installed flashing. This sealant is smoothed out to create a continuous watertight seal, especially in areas where the flashing meets the chimney or in roof valleys where water tends to accumulate.
Final Inspection & Leak Testing: Upon completion of the installation a final inspection is done to ensure all flashing is in place and sealed. Professionals will often perform a leak test by running water around the chimney for several minutes to verify the watertightness of the repair. Any gaps, loose sections or missed spots are addressed immediately.
Cleanup & Monitoring: All debris and leftover materials are cleaned from the work area. Homeowners are advised on how to monitor the repaired flashing especially after heavy rainfall to ensure it continues to function. For many flashing problems especially those with extensive damage or older materials a full replacement is often the more durable and cost effective long term solution compared to patching. Professionals recommend replacement when necessary not as an extra cost but as a better more durable solution that prevents future problems and provides more long term value and peace of mind. This comprehensive approach with specialized knowledge and safety protocols solidifies the value proposition of professional services so the repair is done correctly and effectively and prevents future issues and homeowner safety.
Maintaining Your Flashing: Best Practices for Long Term Protection
Proactive maintenance is the key to ensuring the longevity and effectiveness of your chimney flashing and by extension the entire roof system. Scheduling annual inspections is crucial to catch potential issues early and keep the flashing and chimney functioning properly. Regular inspection and timely intervention is essential to preserve the integrity of the flashing and prevent costly water damage and wood rot. As part of routine maintenance homeowners should inspect the existing chimney and flashing to ensure everything is in good condition.
The Importance of Proactive Maintenance
Preventative measures are key to maintaining the waterproofing capabilities of the chimney system over time. By monitoring and addressing potential issues homeowners can extend the life of their chimney and roof and save time and money that would otherwise be spent on extensive repairs.
Tips for Homeowners
While professional inspections are necessary homeowners can play a big role in early detection through regular visual checks.
Regular Visual Inspections: Homeowners should make it a habit to visually inspect their roof and chimney including the flashing at least once a year. The best times for these inspections are before the cold weather sets in and especially after any severe weather events like heavy storms or high winds. During these checks homeowners should look for visible signs of trouble such as rust, corrosion, water stains, cracks or any sections of the flashing that appear loose or missing.
Keep the Area Clear: Make sure no debris such as fallen leaves, twigs or other organic matter accumulates around the base of the chimney. Debris can impede the flow of water away from the chimney and cause pooling and water penetration.
Address Issues Quickly: Recognizing flashing damage early and addressing it promptly can save time and money. Ignoring these early signs allows minor problems to compound and become more extensive and expensive.
The Importance of Professional Annual Checks
While homeowner vigilance is the first line of defense professionals provide a second layer of protection. They can conduct thorough inspections that can catch subtle issues or underlying problems that may be missed during a casual visual check. They have the expertise to assess the flashing condition, identify potential weaknesses and ensure any repairs or installations are done correctly to prevent premature failure.
The relationship between homeowner observation and professional expertise is symbiotic. Homeowners are best positioned to notice early warning signs from within their homes or during ground level observations. However translating those observations into accurate diagnoses and effective lasting solutions requires the specialized knowledge and equipment of a professional. Roof Rescue offers expert inspections that can catch problems early and give homeowners peace of mind and potentially save them from costly major repairs down the line by addressing issues before they escalate.
Repair Costs: What Affects Your Investment
Chimney flashing repair costs can vary greatly depending on the complexity of the work, materials involved, and the specifics of each home. On average chimney flashing repair ranges from $400 to $1,600. But for large or natural stone chimneys costs can exceed $2,000. For minor leaks that only require resealing a professional job might cost as little as $200.
Factors That Affect Cost
Several factors contribute to the total cost of chimney flashing repair:
Extent of Damage: The severity of the damage is the biggest factor. Minor leaks that can be fixed by resealing existing flashing are less expensive than situations where extensive damage requires a full flashing replacement. Severe structural issues related to water infiltration will add to the cost.
Flashing Material: The material chosen affects the cost. Copper is the most expensive followed by aluminum and then steel. Each material has different properties in terms of durability, malleability and corrosion resistance which affects its price.
Table 2: Chimney Flashing Materials Cost Comparison
Material | Cost (Per Linear Foot) |
---|---|
Steel | $0.50 |
Aluminum | $0.75 |
Copper | $2 – $3 |
Chimney Size and Type: Larger chimneys require more material and labor for flashing installation. And the material of the chimney itself plays a role. Natural stone chimneys are more difficult to work with than manufactured veneer chimneys so labor costs are higher.
Roof Configuration & Accessibility: The design of the roof and the chimney itself affects labor costs. High pitch roofs, multi-story homes or chimneys with unusual shapes or configurations require more complex safety setups and specialized techniques so labor time and cost increases.
Labor Costs: Labor is a big part of the total repair cost. Professional masons or chimney sweeps charge an average of $75 per hour but rates can vary regionally from $50 to $150 per hour. Urban areas have higher labor rates due to higher demand and cost of living.
Type of Flashing System: The type of flashing system used also affects the price. Continuous flashing which is a single strip of metal bent to fit the chimney and roof is more complex and expensive to install than step flashing but often more durable and leak proof.
Related Costs
Homeowners should also be aware that a chimney flashing repair might not be a standalone cost. Often flashing issues are symptoms of broader problems with the chimney or roof which may require additional repairs. These “hidden costs” can include:
Chimney Inspection: A basic chimney inspection costs between $80 and $200 often bundled with a chimney cleaning. But a comprehensive inspection to diagnose serious structural damage can cost up to $5,000.
Chimney Cleaning: Annual chimney cleaning is recommended and costs between $130 and $380.12
Repointing: If mortar joints around the chimney have deteriorated due to water infiltration, tuckpointing (repainting) small areas of damaged mortar can cost between $500 and $2,500 depending on the scope.* Waterproofing: Waterproofing applications can cost around $200 to $500.
Chimney Cap or Crown Damage Repair: Issues with the chimney cap or crown which also protect against water intrusion may need to be addressed.
Roof Inspection: If leaks are present a roof inspection may be needed which can cost between $75 and $800.
It’s important to understand these related costs. A professional assessment by Roof Rescue gives you a complete picture of the problem, not just the flashing issue but also any underlying causes or damage to other components. This way you get a complete and lasting solution not piecemeal fixes that don’t address the root cause and lead to more problems.
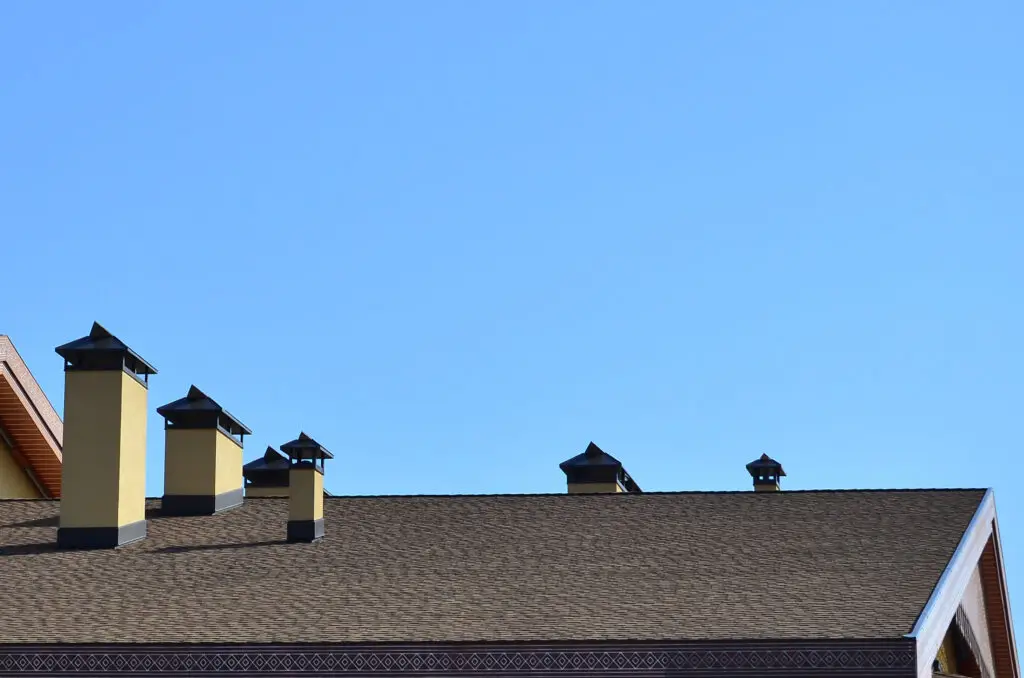
Protect Your Home: Call Roof Rescue Today!
The evidence shows chimney flashing is more than just a component; it’s an investment in the long term protection, structural integrity, energy efficiency and value of your home. Ignoring even minor flashing issues can trigger a chain of events that leads to structural damage, health hazards from mold and ultimately higher repair costs.
Roof Rescue has unparalleled expertise in chimney flashing repair and maintenance. Our professionals are skilled in diagnosis, safe and effective repair or replacement techniques and have a deep understanding of the technical details such as material compatibility and installation methods. So every repair is not just a temporary fix but a durable long lasting solution for your home.
Choosing professional intervention gives you peace of mind. Given the dangers and technical complexities of roof work, entrusting your chimney flashing to certified experts means the job will be done right and safe the first time. This proactive investment protects your property from the elements and prevents the “cost of inaction” from turning a manageable issue into a major problem.
Don’t wait for visible leaks or significant damage to appear. Protect your home and your investment today. Contact Roof Rescue for a chimney flashing inspection. Our team is ready to give you the expert assessment and solutions you need to protect your home.
Frequently Asked Questions
What is chimney flashing repair?
Chimney flashing repair involves restoring or replacing the specialized metal components—such as step flashing and counter flashing—that create a watertight seal at the junction where the chimney meets the roof. These elements, typically made from durable metals like copper, stainless steel, or aluminum, are designed to redirect rain and melting snow away from the chimney and roof interface to prevent leaks, wood rot, mold growth, and structural damage. This process restores your home’s protective barrier against water intrusion and enhances roof and chimney protection, energy efficiency, and long-term integrity.
How much does chimney flashing repair cost?
The cost of chimney flashing repair varies depending on the damage extent, materials used, and complexity of the job:
- According to Roof Rescue USA, repairs typically range from $400 to $1,600, and may exceed $2,000 for large or natural stone chimneys. Minor resealing work could cost as little as $200.
- Angi’s List confirms a similar average range of $400 to $1,600, with the possibility of higher costs for larger chimneys.
- HomeGuide reports flashing repair costs between $200 to $500, and full flashing replacements from $300 to $1,500, depending on chimney type and size.
- A more recent 2025 estimate suggests nationwide averages between $300 to $700 for flashing repair, with minor repairs costing $150 to $300, and full replacements ranging $800 to $1,500+.
How to repair chimney flashing?
A professional chimney flashing repair typically follows a structured, multi-step process:
- Inspection & Assessment: Identify damage like rust, gaps, or leaks.
- Removal: Carefully lift out old flashing without damaging the chimney or roof.
- Install Step Flashing: Layer L-shaped flashing pieces under shingles, overlapping to create a water-shedding cascade.
- Install Counter Flashing: Secure vertical flashing over the step flashing, embedding into the chimney’s mortar or fastening to the masonry, then seal the top edge to prevent water infiltration.
- Seal Joints: Apply roofing cement or sealant (and roofing tar, if needed) to nail heads and gaps to ensure a watertight barrier.
- Final Inspection: Test for leaks, often by simulating rain, to verify the integrity of the repair.
Do roofing companies replace flashing?
Yes. Roofing contractors routinely inspect and, if necessary, replace flashing during roof repairs or replacements. If existing flashing is rusted, has holes, or is separated from the roof, it needs to be replaced. Even if it’s currently intact, replacing flashing along with the roof can save time and money in the long run, preventing future leaks and complications.
Can you replace chimney flashing without replacing shingles?
It depends on the flashing condition and approach. In some cases—like minor leaks—a resealing of the existing flashing can suffice. However, many repairs require lifting shingles to install or replace flashing properly to ensure a watertight seal. If flashing is in poor condition, replacing it—even if it means disturbing shingles—is usually recommended for long-term effectiveness.
How long does it take to fix chimney flashing?
The Roof Rescue USA article doesn’t specify exact timelines, but chimney flashing repair is typically a multi-step process involving inspection, removal, installation, sealing, and leak testing—all of which require professional precision and safety precautions. In practice, a straightforward repair may span a single day including drying time, while full replacements or complex flashing systems could take longer depending on roof pitch, accessibility, and weather conditions.

Mark Franklin, owner of Roof Rescue in Idaho Falls, Idaho, has been a trusted name in roofing since 2014. Serving Idaho, Montana, Wyoming, and Utah, Roof Rescue specializes in commercial and residential roof replacement and installation. Recognized for community initiatives like the “Operation Roof Rescue” program, which provides free roofs to local heroes, Mark combines professionalism with a passion for giving back. With 16 years of industry experience, an A+ Better Business Bureau rating, and glowing customer reviews, Mark’s leadership embodies quality and community-focused service.